Posts
As of April this year, the MPA series of electronic pipettes, which took two years of development, have been on the market for one year. Putting this new product out on the pipette market this past year has been quite the challenge. I traveled from Kyushu to Hokkaido and even abroad to market the product in development as it was decided that the MPA series would have difficulties penetrating markets still critical of electronic pipettes on our existing sales routes.
It was quite demanding to carry out sales promotions while making progress with our various development projects. The only consolation was that I was determined to take responsibility for the results of my plans. The fact that the development of weighing instruments stagnated as a result of investing in pipette development is something I ruminate on time to time.
I was worried that perhaps the MPA series would not sell more than a few hundred units in the first year. However, once sales began my outlook became more positive. I was also surprised at how dramatic the drawing power of our electronic pipette lineup was at exhibitions. Although the real sales expansion has yet to begin I learned there was significant demand for charging stands and multichannel and 10 mL pipettes from visiting the various markets.
Using this information we proceeded to simultaneously develop a linkable single pipette charging stand and a four pipette charging stand. We also produced a charging hanger that allows a device to be placed anywhere as well as a hanger without the charging feature.
Our next development priority was to make a 10 mL pipette. We had two reasons for our swift development of the 10 mL pipette. First the goal of the MPA series was to replace existing sales of manual pipettes, which currently prevail in the market. Secondly some operations on manual 5 mL and 10 mL pipettes place a burden on researchers as they require a great deal of effort to use because of the large diameter of the cylinder and long movements of the piston.
To increase the volume of a pipette, it is necessary to increase the size of the piston. However, if we were to make our existing MPA-1200 piston larger the internal radius of the O-ring that seals the piston would become too big, and the required operational force would exceed the output of the motor. Additionally enlarging the inside diameter of the O-ring would increase the risk of air leakage. So we introduced U-packing (a component with a cross section that looks like the letter ‘U’ and is often used in hydropneumatic cylinders) to the piston side. My six years of experience with a pneumatic equipment manufacturer helped us make this change to the specifications.
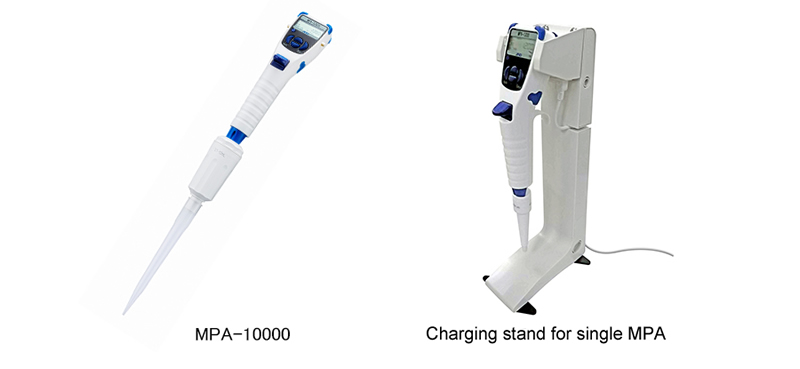
It is from myriad experiences that people become better able to adapt to challenges that lie before them. Below I’d like to take some time to tell a personal story. When I was in college I went to RIKEN, an independent research facility, for my graduation research. At that time, my lecturer at Nihon University, Dr. Takamatsu, was also a researcher at RIKEN. Through him I was given the opportunity to join the Biological Macromolecular Physics Laboratory at RIKEN. My lab manager was Dr. Fukada who would go on to be the director of RIKEN. I was in charge of experiments dealing with the piezoelectric properties of PVDF (a fluorocarbon polymer). The reason I chose RIKEN was that compared my school in Setagaya, Wakō, where RIKEN is located, was closer to my home. Also at that time I wasn’t particularly fond of the school system. As a student who never studied hard and had no major ambitions I was a burden on RIKEN and must have caused them many problems.
Somehow I completed my graduation research. When I was searching for jobs Dr. Takamatsu introduced me to a manufacturer of blood vessels made from fluorocarbon polymers. Not wanting to be a cog in a large cooperation I had the desire to work for a middle sized corporation, so I applied, took the test and interview, and was hired to that company.
Immediately after completing introductory training I was dispatched to a subsidiary facility established three years prior in Okayama. At the interview I was asked “How do you feel about working in Okayama?” to which I responded that I had no problems. Afterwards I found out that out of the 20 people who joined the company at that time, the two that were sent to Okayama were the only 2 that said they would be comfortable going to Okayama.
The thing that was most surprising to me about my dispatch location was that even though it was on a major train line, trains only came to the closest station once an hour. In front of the station was a rundown inn among some residences. After transferring in Okayama I was the only person on the train that led to the inn on the evening before my first day of work. After 30 minutes of riding through the pitch-black night loneliness finally got to me and I began to wonder if I had made a mistake coming to this remote place. Apparently the coworkers waiting for me at the inn thought I had quit since I arrived so late.
During my time in that rural area I remember one occasion when everyone was talking about how I liked ramen noodles. I thought this was strange but then I remember mentioning to a coworker that I have instant ramen for breakfast when there is nothing else to eat. This was my first-hand experience of how fast news spreads in the countryside. The facility I worked in produced waterproofing and breathable material for hiking clothing. One of my responsibilities was that every morning I had to alternate wearing our products and our competitor’s products, go running, and write a detailed report about the breathability of the products.
I quit the job in Okayama in December of that year. Thinking about it now, quitting only half a year in because I didn’t care for the work or my assigned location was an extremely selfish thing to do. I went to tell Dr. Takamatsu, the man introduced me to that company, that I had quit. He scolded me for quitting the job in such a short amount of time. He said it was inconsiderate to the younger students as many graduates from the lab had taken and failed the entrance exam for that company in the past. Nevertheless, he offered to introduce such an impossible student as myself to another company. But I thought that I would never be able to quit the second time and refused.
I went on to take employment tests for many companies but I couldn’t find one that wanted to hire a person who quit their first job half a year in. Eventually I found myself on unemployment insurance. Actually receiving the money panicked me. I thought that if I keep this up I’ll never have a future and prioritized searching for a new job.
A few months later I found employment in the engine design department in a subsidiary of the internal combustion engine department of Niigata Engineering, the maker of the first diesel engines in Japan. It was a short two years but during this time I used analytical tools based on the finite element method and analyzed the strength of crankcases and connecting rods. This was the time when PCs were starting to appear in the manufacturing industry. So I read a few books and used knowledge I acquired from them as well as the computer given to me to make programs based on the finite element method. I pushed forward with my work assertively and because I did it from my own volition I studied more during this time than I had any time up until this point in my life.
Niigata Engineering Co. Ltd, a company with 5000 employees and their own health insurance union, went bankrupt some years after I quit. I watched Muramatsu, the head of the internal combustion engine department at that time, acting as the last president hold a conference on bankruptcy on television. Although I had seen it coming, I realized that even large company with a long history and plenty of assets will eventually go bankrupt if profits fail to materialize.
I then went on to work for a pneumatic equipment manufacturer for six years. There were two different people in charge of electrical and mechanical designs. As a result, research could not progress on essential components such as rubber seals or solenoids for electric valves. This was because these components are neither electric nor mechanical but rather their own category. And so, right after entering the company, me, with a background in physics and no area of expertise would oversee research on both types of components. I still remember the puzzled look on my superiors face after immediately accepting the job that no one wanted to do.
I took the “Entry Level Rubber Training” course at the Chemicals Evaluation and Research Institute, Japan (CERIJ) in Mukojima to learn about the fundamentals of rubber. Over several months I received practical training starting with the roller-based kneading of rubber materials. I used this newly acquired knowledge and a finite element method program I made to perform deformation analyses of rubber seals. Subsequently I went on to study magnetic circuits independently and produce a magnet field analysis program and applied it to our designs. After a period of time I became the leading engineer in these two fields of the company. It was here that I came to realize that knowledge from a previous job could be put to work on future job.
Thereafter I joined A&D and managed the development of electromagnetic equilibrium balances as an expert on magnetic circuits. In no time at all 26 years passed. I believe that my positive approach to the work given to me has helped me to understand a variety of technical information. I think that short stays at various companies and the experiences gained from the different environments were good for me and in the end helped to broaden my understanding of technology. From my experiences, I believe that especially when one is young and had no work skills, it is almost impossible to find one’s true calling.
If you decide that your work environment isn’t right you should move on to the next job without waiting too long. However once your mind has had a chance to mature and you have even a slight bit of interest in work, you should use that chance to try your hardest. It is not a good idea to set out on an endless search to find true happiness; instead I believe it is important to use the environment given to you and work hard until it feels like your calling.
Even though the fruit of your efforts don’t materialize immediately, you will gain more confidence and eventually be rewarded. I am fortunate that I was able to learn that through my own career.
Now let’s return to the MPA-10000.
In the MPA-10000 we achieved success by using a highly regarded U-packing, lowering the drive force required to move the piston and improving the sealing ability. We originally believed that developing both 5 mL and 10 mL pipettes would be necessary; however, by using the electronic pipette’s high base level of performance to our advantage we decided that we could surpass the function of two manual devices with one electric pipette.
The MPA-10000 demonstrates its true power when used for preparing a large number of samples or reagents for analysis, as it is capable of dispensing 100 μL 99 times from a single aspiration. I believe this device will be incredibly useful for researchers and inspection personnel who before had to bear the brunt of the work of dispensing large volumes repeatedly with a manual pipette.
About five years ago, at the start of this Development Stories series, I wrote about management tools for micropipettes. In this first Development Story of 2015, I will summarize the development process behind our unique recharging device for our electronic micropipettes. I apologize for the delay in releasing this article, which was almost finished in October of last year, but the last days of 2014 turned into quite a busy time for me, both at work and at home, and progress was stalled for about three months.
Micropipettes are devices that are used without fail in fields that employ analytical balances, which are typified by microbalances. The “electronic” single-channel pipette, which is perceived in this pipette market as being an “unsellable” device, is said to only hold an insignificant 1% market share in Japan. Nevertheless, A&D has daringly set about developing an electronic single-channel pipette as a brand new product and has now released this in the market. Pipettes are uncharted territory for A&D and mean entering a new market for us. In order to compete in a market with no previous results, we designed an original pipette and carefully planned the product development schedule right through to mass production. However, people’s views on this new – and perhaps even foolhardy – challenge of gaining a foothold, and then hopefully a strong reputation, in this pipette market were pessimistic to say the least. We were even told, by people both within and outside A&D who were knowledgeable in this industry, that we had no right to be successful in this new enterprise and it was doomed to failure! Even within A&D, we had hardly any advocates at the beginning for embarking on such a tough journey, and to be honest, not even I had any strong self-assurance that we would be able to sell our newly developed pipette.
A regular thought I have is that development of a new product with previously unavailable functionality or breaking into a new market is a lot like climbing a mountain. When I mention mountain climbing here I am referring not so much to any technical challenges, but the sense of adventure that grips certain people and compels them to venture into the wilds and potential risk. If you define sense of adventure as moving into an unknown field, adventurous mountain climbing means that if your technical ability, strength or ability to reflect upon previous experiences is lacking, you are unlikely to make it to the top. Even supposing that you could make it to the summit, a safe descent is far from guaranteed. For new product development, when attempting development in a new field or developing products with more sophisticated functionality and performance than ever before, your efforts can easily end in failure. Therefore, for both pursuits, it is essential to set your goals properly at the beginning, apply an indispensable risk management approach to preliminary research and target achievements, and acquire a new set of skills and techniques. It is also vital to be able to handle a variety of problems or changes in circumstances and to approach the goals with flexible skills for handling these matters. In addition to these important criteria, perseverance when faced with difficulties and a “never-say-die” attitude will often result in success.
However, among all of the factors that contribute to success or failure, I think the most important criterion is personally having the passion to want to create a new product or to make it to the summit of a mountain.
Speaking from personal experiences, even if you fail in your attempts at product development or mountain climbing, if you put in as much effort as you can in the circumstances, the chances of tasting success the next time are very high. This is testimony to the fact that the only real way people have of learning is through their failures and that if we critically and objectively analyze our own experiences in failure and can take them on board, we have a much higher chance of success at our next attempt.
One of the goals we set ourselves for development of an electronic pipette was to stick to our own brand. About six years ago, we started selling devices for pipette quality and performance management. Since then, from our experiences in all the relevant stages – from planning through development to sales – of those products, we have been aware of the underlying problems of manual pipettes which currently dominate the market. Further, as a result of considerable market research before embarking on development, we also had a clear idea of what the problems were for existing electronic pipettes. From all these, we came to the conclusion that we had to develop a new type of electronic pipette which was highly unique and addressed all of the problems that could potentially occur in the actual places of use.
The newly developed electronic pipette was recognized as having high precision in multiple dispensing, being durable and hard to break, and being simple to operate with practically no risk of incurring repetitive strain injury. This led to it earning a reputation beyond even our own expectations. Once development of the unit itself was finished, the next problem we turned our minds to was the need to develop a convenient charging device which could keep the pipette in an upright position and allow simple charging in that state. All of the existing electronic pipette chargers were large standing types which allowed simultaneous charging of about four pipettes at a time.
Visiting a few laboratories for our own research, we found that existing chargers occupied a large space on the laboratory table, generally cost nearly as much as the pipettes themselves, and seemed to reduce the amount of freedom researchers had for installation. So with the assumption that researchers had a dearth of free space upon their laboratory tables, we set about developing a charging hanger which could be placed in any location they wanted. Our charging hanger was devised as having a similar form to manual pipette hangers, but with additional charging functionality. It should be a compact design which could be attached anywhere, such as the side of the laboratory table or to a medicine rack, etc., and also be capable of linking several units to the same power source for simultaneous charging. Keeping these specifications as our goals, we released a charger hanger for an electronic pipette onto the laboratory market with unprecedented ease of use, which could be freely placed anywhere at the user’s convenience, took up little space, and allowed use of multiple units at the same time.
I should share a few more details of our newly developed charging hanger. While offering a space where our MPA Series pipettes can be kept in a vertical position, the MPA pipette will start to be automatically recharged as soon as it is placed. Therefore when research work is wrapped up in the evening, by simply hanging the MPA pipette in its holder before returning home, the pipette will be fully recharged the next morning when you return to work, available for use straight away.
In general, one user uses more than one pipette, so we made it possible to recharge multiple MPA pipettes simultaneously by lining up multiple charging hangers. As it would be extremely cumbersome to have multiple units each connected separately to the AC power supply, once supplying power to one of those hanger units it can act as the “parent” hanger, with subsequent “child” units being connected to this first one by linking cables. It is also possible to confirm the hangers are receiving power by an LED light on the top of the hanger which illuminates when power is flowing. With this development it is possible to avoid the risk of all hangers going out of action if one of the consecutively wired hangers was to fail for some reason. A&D has applied for patents for these previously unavailable functionalities. By commercializing such products as this, we hope to continue pursuing and proposing convenience in laboratories around the world.
I believe that with the combined use of the MPA Series and their charging hangers we have established a simple method of use for pipetting work in the laboratory which is more accurate, places no strain on the user’s hands and offers a simple technique for recharging. From here on, I would like to continue growing this range of products even further with pipettes with increased capacity, multiple-channel types, connectable pipette stands and other further developments.
In the more than 100 years since Louis Pasteur’s breakthroughs establishing the field of microbiology, Western medicine has advanced remarkably to its present sophisticated levels. With its origins in the glass pipette, the micropipette, capable of measuring minute amounts of liquids to a high degree of precision, has been one of the essential tools in supporting these achievements, as a requisite piece of equipment in a biotechnology lab.
Presently, over 100,000 micropipettes are sold in Japan every year, and worldwide sales amount to over a million. Major pharmaceutical firms will often have several thousand micropipettes at just one of their main research laboratories. Micropipettes’ two most valuable characteristics are their ability to dispense tiny amounts of liquids, together with the easy handling provided by disposable pipette tips, which retain the sample being measured via air pressure, providing a reduction in occurrences of pipette contamination and also of the laborious process of cleaning pipettes. As a result, it could be said that micropipettes have made a significant contribution to improving the quality and productivity of testing and inspecting processes and are an indispensable tool in many aspects of biotechnology, pharmaceutical, foodstuff and clinical research.
While this convenience of use has meant the micropipette has come to be used in a wide variety of situations around the world, it would be hard to say there is a firmly established method for micropipette management. One of the reasons for this is the lack of an established method for managing its volumes as a quantity-measuring device. For example, while pipettes can determine volume, they are different from weighing machines in that they do not use weights or equivalent which can act as a reference standard for managing volume. This could be considered a very serious problem. Presently in pipette makers’ reports of results, volume (V) is determined from a calculation of V = m ÷ρ, where the coefficient of ρ is the density of purified water, which is a known quantity, and mass (m) is found by dispensing the purified water with a pipette on the tray of a balance and reading the displayed amount. However, the density of the water will change according to its temperature, so it is necessary to perform density correction at each different temperature. Another problem that could arise in practice is the pipette user dispensing a liquid other than water, with a different density. Further, the viscosity of water at 20°C of 1.002 mPa•s is extremely small and even a water solution with 50% glycerol will result in a viscosity level several times higher than purified water. Therefore, even if the pipette is calibrated with water, the density and viscosity of the liquid that is actually dispensed could differ from calibrated water and the interchangeability of the volumes will not be ensured, due to differences in the viscous resistance.
With micropipettes, the differences in air pressure created by the movement of the built-in piston are used for aspirating and dispensing of the liquid. Therefore, even with the same volume settings, differences in volumes will occur not only due to the viscosity and density of the liquid, but also the shape and material used for the tip. It is probably quite clear then, that with these conditions influencing measurement, dispensing volumes which differ from the pipette’s report of results is a quite a concern in many cases.
Besides such technical problems, there are also problems connected to the method of use of the pipette user. Namely, there are often individual differences in the manner of operation between users, as the pipette is held in the hand all day and it is also a very small tool to handle. Further, when the pipette is dropped from a desk or the hand, these kinds of impact loads can cause deformations in the operating rod or damage to the structure, which is associated with a reduction in precision in dispensed volumes.
With considerations such as these ones above, I started to have doubts about current pipette management techniques and thought about what kind of management methods should be used for pipettes under normal circumstances. For example, while you could say that having the pipette maker issue a calibration report once or twice a year is an important management technique, it is unrealistic to confidently assert that traceability or validation can be ensured in between periodic inspections that only occur once or twice a year. Further, even if calibration is performed with purified water and the tip specified by the manufacturer, there are other variations that can occur at the place of use other than the constitution of the liquid or the type of tip used, such as influences of the measurement environment or the degree of expertise of the user. I could only come to the conclusion that it is difficult to ensure traceability in the place of measurement with just the pipette maker’s report of results used for reference. Next, considering a solution to these problems, I was able to put my many years of experience in development of weighing devices to work by summarizing my proposed measures into the following two points:
1. As a precision weighing device manufacturer, we have a duty to provide to the market a management tool which can allow daily and periodic checks of pipettes at their place of use.
2. A new pipette is needed which allows pipette calibration management that reflects the actual conditions it is used under.
These two points above would be satisfied by providing, for example, devices that allow testing the pipette at the place of use when any kind of trouble eventuates, such as dropping it or aspirating too much liquid; a pipette equipped with a calibration function that applies the tip and liquid used, making it easy to perform calibration that actually fits the conditions at the place of use; and measures by which pipette maintenance can be performed easily by the user themselves.
As a result of the considerations mentioned above, in April this year A&D became the first manufacturer in Japan to release a general-use electronic pipette. Preceding this, we also developed a pipette leak tester and accuracy (volume) tester for pipette users five years ago. Using these management tools, it has become possible to create standard operating procedures (SOP) for pipette management to be carried out by users themselves. Further, we have also recently developed the AD-1695 dedicated pipette management tool which does not require the use of a PC. As the AD-1695 allows interactive operation with its graphic user interface, daily and periodic checks of the pipette can be performed with ease at user level.
Our newly released original electronic pipette is equipped with calibration functionality in µl units and allows volume calibration by users themselves. For calibration in µl units with liquids other than water, difficult density measurement of the liquid is required. To help with this, we have also added a new calibration and display function with mg values. By performing measurement and calibration of volume with mg units, measurement and correction of density is no longer required and pipette calibration can then be performed using the mg value displayed by the balance. Having a uniform unit of mg for measurement and calibration means calibration with the liquid and tip to be actually used becomes much easier to perform, and means that a mixture consisting of a measured amount of powder and liquid can be simply and accurately calculated by weight ratio.
With the MPA series of electronic pipettes, the lower part of the device including the piston, which is often subject to contamination, and the main part of the pipette (control and drive parts) are designed as separate units, so can be easily detached from each other. Therefore, sterilization using an autoclave is now possible for the lower part only, and due to the design of the MPA series this part can also be simply disposed of and replaced by anyone when contamination or wear occurs.
As a result of our considerations over the last five years, I think that we have finally achieved a range of nearly ideal micropipettes and accompanying management tools that offer practical solutions for the actual conditions that are encountered in everyday pipette use. I hope that these devices can be used both as an aid to creating SOPs for those responsible for pipette management and also as effective tools for ensuring safe and reassuring use for pipette users. A&D has already prepared original guidelines and documents on these subjects that enable simple creation of SOPs for pipette management. Please feel free to contact us at any time to discuss any matters relating to our pipettes and pipette management tools.
In spring this year, A&D launched our new MPA Series of original electronic single channel pipettes. With our exciting new products in hand, we visited research laboratories across Japan to explain their many benefits, starting in Kyushu’s Fukuoka, then moving to Shikoku Island, Osaka, Kyoto, Nagoya, the Hokuriku region, then finally areas in around Tokyo. Our promotional activities have already extended overseas as well, introducing the MPA Series to laboratories in Korea and conducting some market research there.
In this Development Story, I will summarize what we have learned from this market research and propose practical solutions to some of the problems that pipette users are facing in their place of work.
- Dispensing liquids with a high level of viscosity
If the viscosity of the dispensed liquid is high, it sticks to the outer perimeter and inner surface of the tip. Liquids that particularly pose a problem are those that stick to the inner wall of the tip. When this happens it is not possible to cleanly discharge or ensure accurate dispensing amounts. Addressing this problem requires, 1) slowing down the aspirating and dispensing speeds so the liquid can be properly transferred; 2) aspirating a larger amount of the liquid beforehand and establishing the dispensed amount based on the amount discharged (this is commonly called reverse mode and reduces the degree of error with the liquid that remains inside the tip); 3) using a tip with a wide circumference to reduce the pressure added to the high viscosity liquid. MPA electronic pipettes have five different speeds of aspiration and dispensing selectable and can be easily set to reverse mode, making more stable dispensing possible.
However, whichever of these methods is used, dispensing liquids with viscosities around 10 times higher than water (10 mPa•s) will always be a problem for micropipettes which rely on air pressure for their operation. A type of dispensing device that has a piston attach the liquid would have to be used for any viscosity level higher than this.
- Dispensing highly volatile liquids such as solvents
Many researchers feel that the dispensing of highly volatile and low viscosity liquids such as solvents is rather difficult. The cause of this problem is the empty space in the cylinder built into the pipette becoming filled with vapour from the solvent or other volatile liquid. In other words, as soon as the solvent is aspirated the piston is filled with vapour from the solvent, which increases pressure inside the cylinder and forces the solvent to leak out of the tip or makes the dispensing amount inconsistent. In order to avoid this phenomenon, it is recommended to aspirate and discharge the solvent several times before the dispensing is performed to create a constant vapour pressure. This so-called “pre-rinse” practice is recommended for not only solvents, but as an effective general preparation measure to ensure the accuracy of the dispensing process. One of the MPA Series’ many merits is simple switch-only operation of multiple aspiration-discharge actions which are effective for mixing liquids or performing pre-rinse.
- Operability when performing consecutive dispensing
Dispensing to a 96-well microplate is a difficult operation and even if a multiple channel pipette is used, a high degree of skill and dexterity is required to ensure correct dispensing amounts. When a manual single channel pipette is used for repeated dispensing, the same parallel movement of aspirating and dispensing is needed to be done many times, a frustrating task for the researcher and one which can consume a significant amount of time. With an electronic single channel pipette however, with one touch of the switch an amount equivalent to fill 8 or 12 wells can be aspirated in one go, then evenly dispensed with 8 or 12 touches. Particularly when very precise dispensing is required or when there is a need to reduce wasted use of an expensive solution, using an electronic single channel pipette, which provides easy operation and high accuracy, is shown to be the most effective measure.
- Consecutive dispensing with an electronic pipette
When multiple dispensing is performed with an electronic pipette, even amounts cannot be ensured and the first time can be a touch short. We also regularly hear that the final dispensed amount can also be insufficient among other complaints. These issues can also occur with manual-type pipettes in principle, however as multiple dispensing cannot be performed with manual pipettes each dispensed amount cannot truly be compared with others and is therefore not acknowledged as a problem.
The cause of this error in multiple dispensing could be explained as a phenomenon generally called “backlash”. Simply put, this is the same as backlash in the steering wheel of a vehicle. Backlash occurs in the steering wheel of a vehicle when it stops moving in one direction and then starts moving in another, with a delayed response due to gaps between the gears or screws. For pipettes, backlash is caused by the looseness of the screw that controls the variable volume as well as slight shifts in position of parts, such as the o-ring for sealing the cylinder, due to variances in pressure between the negative pressure when aspirating and the application of pressure when dispensing, resulting in changes in volume.
From the explanation above, it can be understood that backlash occurs in both manual and electronic pipettes. For manual pipettes, this occurrence of backlash cannot be resolved. However, for electronic pipettes, it can be avoided. This is because the dispensing amount can be stabilized by aspirating more liquid than is required and before dispensing the liquid automatically discharging a minute amount. In the MPA series, we call this function “pre-dispense” and it comes as standard on all models. We are currently applying for patents and trademarks for this function, but meanwhile, with the addition of this function to the MPA Series, the problem of measurement error in the first dispense of multiple dispensing operations typically seen in previous electronic pipettes has been successfully minimized.
With use of this “pre-dispense” function, we have achieved an enormous improvement in dispensing performance, halving the degree of repeatability compared to manual pipettes manufactured by major pipette makers. I’m intending to report concrete details on this in an academic conference in 2014.
- Compatibility between pipettes and tips
Visiting several research laboratories, we were asked every time about compatibility with tips that are already being used. We insisted that the MPA Series is compatible with existing tips, but the researchers we spoke to were not interested in general terms, but rather in the compatibility with the very tip that they were presently using in their own laboratory. We therefore saw the need to try fitting the MPA Series with most of the tips presently available in the market and check if they deliver accurate dispensing without any leaks. The results are published on our website. From the results of our tests we can say that, with the exception of special tips developed for use only with certain devices, any tip can be used with the MPA Series. However, in tip types with a long overall length, a slight loss in the dispensing amount was noticed. Nevertheless, even in cases such as this, one of the advantages of the MPA series being electronic pipettes is that digital calibration can be easily performed by the user in microliters, or in milligrams like balances. As they can be calibrated at their place of use, the accuracy of the MPA Series can be guaranteed and they can be used with complete peace of mind. (An application for a patent for the digital calibration function of the MPA Series has also been lodged)
- Breakdown and maintenance
It is generally known that a pipette is a device that will break if it is dropped. For manual pipettes, the push-down axle bending or the base part of the tip holder breaking are commonly reported breaks. There are also problems associated with the user aspirating too much of the liquid leading to rust or corrosion of the piston. With electronic pipettes, there have been many reported cases of the display or even the entire device not working after a fall, which has hindered any increase in sales of these devices. In order to protect what could be called the weak spot on an electronic pipette – the display section at the top – the MPA Series features specialized protectors on each four corners of the head section. The design of these patent-pending protectors realizes highly effective durability for the MPA Series, achieving shock resistance from a 1 meter drop when tested dropping the MPA Series onto a P-tile on a concrete base from that height. There is also no chance of over-aspirations from operation errors, as all aspirations are automatic.
The maintenance of the MPA Series is limited to the so-called lower part of the device, which includes the tip holder and piston. This part can be easily removed and replaced by the user themselves, with the pipette ready to be used once again straight away after calibration has been performed.
- Pipette management methods
How should pipettes be properly managed in their place of use? We were asked this question on many occasions. Pipettes should be managed in their place of use in accordance with the procedures stated in the document called Standard Operating Procedures (SOP). Broadly speaking, these procedures could be divided into “daily check” and “periodic inspection”, which could be compared to daily checks of a car and official vehicle inspection. Daily check of the pipette includes confirmation that the exterior is undamaged, that there are no problems with its functions like switches, etc., that there are no leaks in the piston area and so forth. Periodic inspection encompasses all the items of a daily check as well as an examination of the performance of the device, which requires validation of amounts measured by the device by either volume or mass. It will be necessary to decide in advance what to do with a faulty device if any problems are detected during these checks and examinations.
As we considered management methods for pipettes at their place of use would be essential in many cases after we sold the MPA Series, we produced a document that acts as a guide to create Standard Operating Procedures. When introducing this document to researchers responsible for management of equipment such as pipettes, we have been receiving extremely positive responses.
Micropipettes are exempted from Good Manufacturing Practices (GMP), with the assumption that they are not used on the manufacturing floor. However, they are in fact vital in such places for quality management, not to mention for research and clinical examinations. We believe that in the future it will be hard to tell the difference between skilled hands and beginners when using these electronic pipettes, with improvements in repeatability even for the former group, and the rate of use of these easy-to-use devices will increase significantly.
A&D, as a manufacturer of measurement instruments, has a background of being the first company to develop and commercialise pipette management tools. And finally, using our know how in the field, we have developed our own unique MPA Series of micropipettes. We are anticipating this MPA Series to achieve significant gains in quality, as well as reductions in the burden of repetitive pipetting work, in research laboratories and clinical trials around the world with its durability, ease of use, and exceptional performance.
In the previous Development Story, the results of market research into the micropipette market were discussed. However, as this occurred before application for intellectual property rights it was not possible to discuss the details of the technology involved in this new product. In this episode I will explain the aims of the development of the MPA Series of electronic pipettes and the functionality we devised to actually realize those aims.
It has been more than half a century since manual pipettes reached their present form. This could be interpreted as meaning manual pipettes that are presently sold in the market are completely perfected pieces of research equipment.
Modern day pipettes firstly move their pistons by the push of a button. They then work using the method of aspirating liquids due to the difference in air pressure created by the movement of the pistons. That is why they are called the air displacement type. These principles are highly praised as a means for measuring and moving liquids both safely and without contamination.
Presently in Japan, manual pipettes for aspirating and dispensing liquids account for 90% of the market, with the remaining 10% coming from electronic pipette sales. Among electronic pipettes, 90% of these are the multiple-channel type, which can have either 8 or 12 tips attached simultaneously. From this market background it can be inferred that the market share for single-channel electronic pipettes is a tiny 1% of total pipette sales volume.
Due to this sales history, we received many opinions from people in the industry along the lines of “Even if you introduce a brand new type of single-channel electronic pipette to the market, this by no means guarantees you’ll be able to sell it!” Wherever we went we heard this same point of view. On the other hand, on occasion we also received comments such as “Even though I understand the convenience of electronic pipettes, sales are not presently increasing in the market and people are still waiting for an electronic device which meets all their needs.”
While at first I was somewhat perplexed by these statements, after hearing them many times over I eventually gained a certain conviction in regards to electronic pipettes. This was that there are quite clear reasons why the market has not welcomed previous electronic pipettes and if these reasons can be removed from the equation, the majority of manual pipettes will be able to be replaced with electronic ones.
If the operation method for the presently predominant manual pipette is considered, the operation button is moved in the axial direction of the movement of the plunger while the pipette is held in the hand, so consequently it is the role of the thumb to operate the up and down movement of the button. When using a manual pipette, in order push down the operation button located at the head of the pipette with the thumb, the thumb must be held out perpendicular to the hand in a vertical direction, then bent horizontally at the joint. In order to properly operate the plunger, a force equivalent to 3 or 4 kg is required at the tip of the thumb.
There is a serious problem when the thumb is made to move like this: it has been designed to only be able to comfortably bend in the direction of the index finger. On the basis of this notion it is easy to come to the conclusion that the operating method of manual pipettes is a big concern from an ergonomic point of view. In fact, you could argue that even a short period of operation is inviting repetitive strain injuries in the thumbs.
With the aim of improving this area of concern with the operation method of the manual pipette, the new MPA Series was developed so that the pipette could be held with all fingers in a natural grasp, with the movement of the plunger able to be controlled with the ball of the index finger while maintaining that natural position.
Testing this new development, it has been verified that no strain occurs at all when aspirating and dispensing water over 3,000 times continuously over a 5 hour period. As a matter of fact, this test was conducted in order to confirm the longevity of the dedicated lithium ion battery, but when I heard that somebody had been made to perform this experiment for 5 hours alone I strongly admonished the person who commissioned the experiment. That is because I became concerned for the person having to actually perform this action continuously for 5 hours, imagining the effort that would be required with a manual pipette. However, when I asked the test participant the following day and heard there was absolutely no problem, I realized my anxiety was completely unwarranted.
When exchanging tips with the MPA, the release button is pushed with the thumb, but the thumb stays in a horizontal direction pushing downwards. The kilogram force required to operate this release button is relatively small, around 600 g, so absolutely no problems were found with this operation either. Incidentally, the kilogram force required to operate the aspirating and dispensing of the pipette with the ball of the index finger is approximately 300 g.
If strain is considered to come not just from the force required for operation, but from the impulse – the force multiplied by the distance displaced (or duration of operation), the strain relating to operation of the piston for the MPA would be equivalent to less than 1/100 of current manual pipettes.
Electronic pipettes are said to be comparatively heavier than manual ones. In fact, the mechanical hardware that makes up the bulk of the weight of pipettes, such as the piston section and the screws that hold it in place, etc. are basically indistinguishable in weight between manual and electronic versions. But by adding the electronic components such as the motor, battery and electric substrate the weight does actually become about 1.5-2 times that of manual pipettes. However, you could say that most of the weight that people perceive is more governed by the center of gravity than the actual weight of the device. In other words, the most important point that should be considered for ease of holding the pipette is how far out the center of gravity of the device is from the axis of grip created when holding it.
With the MPA series the center of gravity of their weight (approximately 160 g) does not deviate from the axis of grip. Also, the display section was made more compact so that the center of gravity is lowered as much as possible. Thanks to these innovations, anybody holding the MPA for the first time will be pleasantly surprised by its lightness.
In addition to this sensation of lightness, importance has been placed upon the simple, yet specialized, function settings of basic, automatic aspirating and dispensing; multiple dispensing, which is the strong point of electronic pipettes; and a liquid mixing function. Further, it is now possible to select volume display in µL units and weight display in mg units, and the user can now easily perform calibration themselves in each mode. In particular, in mg display mode, by unifying measurement units when mixing liquids and powders, creating reagents or analysis samples, previously troublesome and easy to mess up concentration settings have now become much easier to perform.
The MPA Series is a single channel, adjustable volume electronic pipette. It includes four models of 10/20/200/1200, with the figures indicating the maximum possible volumes for aspirating and dispensing (µL). We hope the MPA Series of electronic pipettes will make a great contribution to a wide variety of fields, from medicine to foodstuffs, new materials or environmental measurement, being put to use creating samples for research, clinical trials or material analysis. We believe the MPA Series can lead to great improvements in productivity, increases in quality and advances in workplace health and safety, by greatly reducing occurrences of problems such as repetitive strain injuries.
For a long time in the past, the balance development team that I belong to was solely focused on the development of weighing devices. Within the field of weighing devices, we were responsible for the development of all types of balances applying electromagnetic sensor technology – from analytical to high-capacity models. As for devices not using an electromagnetic sensor, we handled the commercialization of a 1:60,000 resolution high-precision load cell-type scale, as well as a compact electrostatic capacitance scale, starting from the development of their sensors. On the other hand, the team also has a history of horizontal development of the base technologies used in electromagnetic balances, the redevelopment of a tuning fork vibro viscometer. We even worked on a heat-drying moisture analyzer which uses elements from mass measurement and calibration devices for pipettes which apply the gravimetric method, from early planning stages to development and sales promotion activities after the market launch. I think all of this different work provides examples of both vertical and horizontal product development, focused around base technologies.
All this development points to a direction that a manufacturing company can take in order to expand their operations. That is, focusing efforts around technology owned by the company and developing products which utilize those base technologies. It also demonstrates a plan for introducing new products to a market previously shaped by existing products.
Particularly in the laboratory market that uses balances, the three tools which are held in extremely high regard are the micropipette, the microscope and the analytical balance, which is typified by microbalances. All three of these items are commonly used in a variety of research fields. Having already released a range of microbalance in the market, we have now moved to the development and commercialization of electronic pipettes as strategic products in the laboratory market.
Starting with the pharmaceutical industry, use of micropipettes has spread to a wide range of fields for many different substances, including the biotech or genetic research, clinical trials, foodstuffs and cosmetics industries. They are now considered indispensable tools in the research field. These different fields are certainly markets which will grow in the future and more than 20 pipette makers are already crammed into the international market. A decade or two ago the annual market size for pipettes was around 1 million units per year, but that figure is now considered to have doubled to 2 million per year. However, most of the micropipettes presently being sold are manually operated types. In the research field, many researchers are performing pipette operation all day in order to create reagents or samples for use in various clinical assays, for proliferation of genes, etc. However, in these present circumstances manually operated pipettes could be said to present a number of problems for researchers.
Among the most concerning of these problems could be the risk of tendonitis or repetitive stress injury (RSI) developing on the thumbs of many researchers after repetitive operation over an extended period of time. Another problem is that for accurate dispensing, expert operation is required, and there is an individual variability between operators of up to 10-20% for aspirating and dispensing volumes. This causes variation in the sample size, and as a result, the level of precision in tests drops quite considerably. Moreover, as the amounts being dispensed are relatively small, they are principally used only in laboratories, and not on the production floor, making them not subject to management based on Good Manufacturing Practice (GMP) guidelines. Because of this, in contrast to their importance as a testing device and their frequency of use, they are positioned as a device that is not for use in formal situations and are not given proper management. Further problems include the comparatively high cost of sending pipettes to an outside facility for repair or calibration, the lengthy duration this will take and the fact that traceability cannot be guaranteed in the following half year or year until the next calibration.
The problems mentioned above in relation to pipettes have been recognized for quite some time. However they have a history of being neglected as problems which cannot be solved. In response to this, A&D have taken a head start in the industry and commercialized a tool for volume management based on the gravimetric method using a weighing instrument, which allows compliance with the international standard for pipette management, ISO8655. A&D have also solved perhaps the biggest problem for pipettes of air leaks in the piston section with the release of a leak tester which can identify an air leak in an instant – a consideration which gives the end user a possible technique for self management of pipettes themselves.
And now, we have decided to introduce to the market our own originally-conceived pipette to answer some of the basic problems that are inherent in pipettes.
A&D’s MPA series employs a power-operated system in order to prevent repetitive stress injuries and reduce the influence of individual variances in operation methods between users. There have been many proposed electronic pipettes in the past, but they did not receive very high praise in the market. This was because they were comparatively more expensive than manual pipettes and could not be used when the batteries died. Further, they were easily breakable and there was a high cost in time and money when they had to be repaired. There was also some concern regarding their performance. For models designed for dispensing large volumes, the electronic pipette took longer to do the job than experienced operators with a manual type device. Due to issues such as these, electronic pipettes presently only make up a mere 10% or so of the total pipette market.
In terms of limiting discrepancies in individuals’ pipetting work and the gains in quality this adds to the work process, simplification of dispensing work and prevention of workplace injuries of researchers, electronic pipettes have a great many advantages over manual ones. However considering all the demerits which are also mentioned above, electronic pipettes are still not a popular device for many researchers. Reflecting on these negative aspects mentioned above, new functions have been added to our new design, with an improvement to basic performance, an increase in durability against falls and a record of calibration results which guarantees performance at the time of delivery. We further aimed to improve after sales service by providing an exchange of batteries after the device is in use, lengthening the warranty period and offering replacement devices while the purchased product is being repaired. We also set the price at a level that made it very competitive against manual devices.
By guaranteeing the above product specifications and our additional market services and by introducing new pipette management devices to the market, Standard Operating Procedures (SOPs) essential in the workplace can be properly established and compliance with Good Laboratory Practices (GLP) or Good Manufacturing Practices (GMP) in the place of use is now also a possibility. With the researchers themselves taking responsibility for their pipette management, all gaps in traceability resulting from entrusting management of pipettes to outside organizations can be removed and efficient pipette use and management practice can now be thought of as achievable.
In tomorrow’s laboratory, which will have to fully embrace the globalization of the research field, a full guarantee of traceability and device management which meets various regulatory standards is becoming increasingly important.
We are expecting our new electronic pipette MPA series to fully deliver a significant improvement in quality to the research field, together with our pipette management devices, with new functionality and services which greatly reduce the number of problems which can occur with the use of pipettes.